Flt 4 and 5
- Details
- Written by Kevin Horton
- Hits: 2696
I had hoped to get a test flight off on Wednesday, but there was too much low cloud due to a low pressure system slowly working its way through the area. Same thing on Thursday. But, early Friday morning was a winner, and I zipped out to the airport shortly after sunrise to do a test flight - flight 4. I flew for about an hour, then had to land as a layer of lower cloud started to move in.
I concentrated on engine break-in, and a flutter check out to 200 KIAS. I noted a significant drop in oil pressure as I pushed over to accelerate to 200 kt (the oil pressure decreased by 15 to 25 psi). The only possible explanation I could come up with was the oil moving towards the front of the oil sump due to the -10 degree pitch attitude.
During the pre-flight inspection I noted that the static pressure line going to the alternate static valve had been knocked off, which meant that the static system had been open to cockpit air. I don’t know when this occurred, but it puts the airspeed accuracy test I did on flight three into question.
Today I went back out to the airport first thing in the morning, and got another flight off - flight 5. This one concentrated on engine break-in and airspeed accuracy tests. I crunched some of the hand recorded data, and it looks like the system reads perhaps two knots too fast in the range of 110 to 150 kt. I’ll look at the recorded data later to refine these numbers.
Before this flight, I put two more quarts of oil in the engine. It was down perhaps 1.5 quart from the initial 8 quarts I had put in. With the higher oil quantity, there was no drop in oil pressure during descents at -15 pitch attitude, but perhaps a 5 psi drop at -20 degree pitch attitude. It looks like I’ll need to pay close attention to the oil quantity before doing aerobatics.
I had hoped to get a second flight off today, but the wind came up, gusting to 15 kt at 90 degrees to the runway. I’m sure the aircraft is quite capable of handling this, but I want to ramp up the crosswind limits more slowly that that. Instead, I pulled the cowlings and did a big inspection ahead of the firewall. Then I installed the wheel pants, landing gear leg fairings and landing gear to fuselage intersection fairings.
The landing gear intersection fairings are a builder fabricated part. Mine were built when the wings were not on the aircraft, and I discovered that I the upper edge of the fairings interfered with the wing to fuselage intersection fairiings. I had to remove quite a bit of material from the landing gear intersection fairings to allow them to fit.
Now that the aircraft is in the normal aerodyamic configuration, I can start on the full flight test program. I will concentrate on tests at higher engine power for now, as I am not convinced that the engine break-in is complete. When I pulled the lower spark plugs to inspect them, the plugs on three cylinders showed signs of oil.
I'm up to 5.1 hours of air time now, from 5 flights.
Back Home From 3 Week Vacation in France
- Details
- Written by Kevin Horton
- Hits: 2724
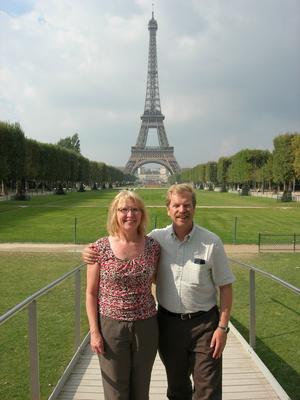
Flt 3 - Data Analysis
- Details
- Written by Kevin Horton
- Hits: 2858
Here are some more notes from flight 3 - the first ones were done in a rush as I was getting ready to head to the airport for a road trip. Now I that finally have a few hours of quiet time this evening, I looked at the data I recorded on flight 3. I found some glitches with the scripts I wrote to record and analyze the data, so it has taken some time to decode it. The process should get faster as I fix the bugs in the scripts.
The aircraft performance appears to be fairly good, especially considering that the wheel pants and landing gear leg fairings are not installed. The rate of climb at 80 KIAS 1000 ft MSL at 30 deg C (density altitude of about 2950 ft) at 1620 lb weight was about 1730 ft/mn. The air was a bit bumpy right after take-off, so this is only an approximate value. This rate of climb is perhaps 120 ft/mn lower than that predicted by a hypothetical performance model I created. It will be interesting to see how the actual performance changes as the engine gets broken in, the excess oil gets sucked out of the air filter, and I put the gear leg fairings and wheel pants on. Maybe my hypothetical performance model is not too far off the mark.
At 4500 ft, 75% power gave about 165 kt TAS (calculated from the IAS value, so this assumes zero error in the airspeed system - that testing is yet to come). Builders generally report an increase of about 15 kt when the wheel pants and gear leg fairings are installed. And, the speed for a given percent power will increase with altitude. So, it looks promising that the aircraft should at least come close to Van's performance figure of 182 kt TAS at 75% power at 8000 ft. Also note that the mixture was full rich for these two conditions - the engine would make more power if the mixture was leaned a bit, and the speed would be a knot or two faster. I think the engine is quite rich at full rich, possibly because I put too much oil on the K&N air filter - I found quite a bit of red filter oil had been sucked into the air induction snorkel after the first flight.
While doing the one hour with power varying between 65% and 75% at 4500 ft, I decided to do one airspeed calibration test point. I did a four leg box pattern at 145 KIAS on the analog ASI, using the event marker to indicate the times of interest in the recorded data (if I am recording data, the trigger on the Infinity stick grip will send an event marker to the recorded data). I analyzed the data later, and really wasn't happy with the quality of two of the legs, as the speed varied more than I would want. But, I averaged the data on each leg, then put the averages into the NTPS spreadsheet - it calculated a TAS of 151.5 kt, with a standard deviation of 0.09 kt, which is extremely low. Maybe too low to be true, considering the apparent poor quality of some of the input data. If I take the TAS of 151.5 kt, and assume a reasonable ram temperature recovery factor on my OAT (the actual recovery factor will be determined on a future test flight), I calculate a CAS of 139.5 kt, which means the airspeed system appears to read about 5 kt too fast at 145 KIAS. This is only one data point, based on somewhat questionable data, so it will be interesting to see how the full set of airspeed calibration tests turn out. Update 6 Oct 08 - I discovered that the static line to the alternate static valve had been knocked off, which was allowing cabin air into the static system. I don't know when this occurred, so I consider the airspeed test from this flight to be invalid.
I did two quick tests to see the rise in EGT at 65% power when leaning from full rich - I wanted to ensure that the engine was not running too lean at full rich. I found that the EGT would increase as below (EGTs are in deg C):
FF EGT1 EGT2 EGT3 EGT412.9 633 648 631 655 # full rich - - - - - 9.3 752 766 748 777 9.2 753 767 749 777 9.1 761 775 755 782 9.0 765 780 757 783 8.9 765 780 757 783 # cylinder 3 peaks 8.8 767 782 757 783 8.7 770 787 752 783 # cylinder 4 peaks 8.6 770 785 757 783 8.5 770 786 757 783 8.4 770 787 755 782 # cylinder 1 peaks 8.3 770 787 754 781 8.2 770 787 752 780 # cylinder 2 peaks 8.1 770 787 752 779 8.0 770 787 749 777 7.9 769 786 746 775 7.8 767 785 745 773
Note that each cylinder had a rise of between 126 to 139 deg C (227 to 250 deg F) which means that full rich mixture was very rich. The cylinders hit peak EGT in a range of 0.7 USG/h fuel flow, which is a bit more than desired for optimum lean of peak EGT operations. Down the road I may work with Airflow Performance to get some injector with different orifice sizes to try to tighten up that spread a bit. Also, when I review the data recorded from the engine monitor, it looks like I need to pull the mixture back a lot more slowly, pausing at each fuel flow to let the EGT values stabilize. I'll repeat this test at various power settings on a future flight.
Flight 3
- Details
- Written by Kevin Horton
- Hits: 3070
I was supposed to fly a check ride in one of the Transport Canada aircraft yesterday afternoon, but it was broken. So, I took a half day of comp time, and went to Smiths Falls to fly the RV-8 instead.
First, I studied the upper cowling attachment to determine why I was having problems installing the long horizontal hinge pins that join it to the lower cowl. First, I put a tiny bit of BoeLube in the leading edge of each hinge eye on the lower cowl, and I put some on the hinge pin. Next, I took a good look at the way the hinge eyes stick past the edge of the upper cowl. I realized that my installation technique was not compatible with the design. I had been starting to align the hinge eyes at the front, and working aft. But, the way that Van says to install the hinge, doing it that way will lead to a condition where you need to give a hard rap of the hand to force the eyes past the edge of the lower cowl a few inches aft of the front. I managed to bend one of the hinge eyes by doing that. I carefully straightened the hinge eye, and from now on I will start the hinge eye alignment at the rear - it makes a big difference. The combination of these two things made a huge difference in the amount of effort to install the lower cowl.
For the flight, I concentrated on engine break-in, following the instructions in Lycoming Service Instruction SI-1427B. It is a long document, but in a nutshell it calls for one hour at 75% power, followed by one hour alternating between 75% and 65%, and then 30 minutes at the manufacturer’s maximum recommended power (whatever that is for an RV). I decided that the two previous flights had effectively been a total of a half hour at a bit more than 75% power, so yesterday I did a two hour flight - a half hour at 4500 ft and 2500 rpm and 24” MP (75% power), followed by an hour alternating between 75% and 2300 rpm and 23” MP (65% power), followed by 30 minutes at 2500 ft at 2700 rpm and full throttle. The engine seemed happy at all conditions, with the CHTs staying below 375 deg F, and the oil temperature hanging around 180 deg F, except at max power, when it got up to about 195 deg F. The OAT at 2500 ft was about 25 deg C (77 deg F).
While I was droning around, I tested the Microair 760 COM reception. It uses an Archer antenna, inside the left wing tip. It was able to clearly pick up ATIS from an airport 50 nm away. The reception was slighty weaker if the station was off the right wing tip, but it was still readable. I didn’t try any long range transmission yet. I also confirmed the NAVs on the GNS430 and Narco 122D were working. And, I spent some time becoming familiar with the pages and menus of the GNS430.
I discovered that my round dial Van’s MP gauge intermittently seems to have died. Hopefully it is just a loose connection. Fortunately I also have MP on the Grand Rapids EIS 4000, and it works well. The Dynon EFIS heading seemed to be reading strangely sometimes. I may need to do another compass calibration - the original one was done with the engine OFF to avoid low power running. After the engine is broken in I’ll do another one with the engine running.
First Flight Video
- Details
- Written by Kevin Horton
- Hits: 3424
Terry videotaped the first flight from the ground. Last night I edited it, and pushed it out to YouTube overnight. It took forever to show up, but here it is.
Thanks to everyone
- Details
- Written by Kevin Horton
- Hits: 3686